В японском промышленном центре заводы компании Toyota (7203.T) используют самоходные сборочные линии, массивное литье под давлением и даже старомодную ручную полировку, в попытке догнать производство аккумуляторных электромобилей, передает Bizmedia.kz.
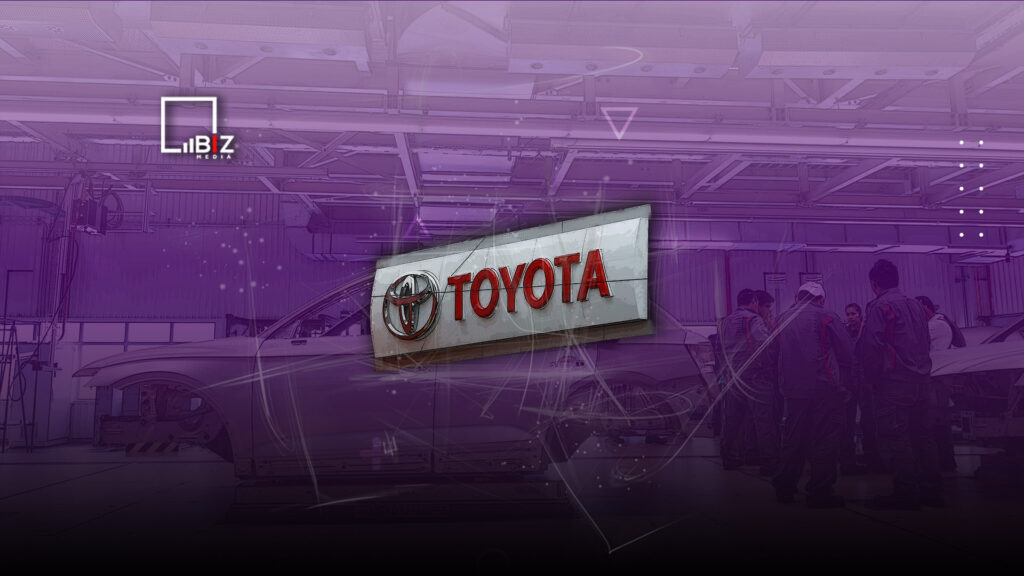
Как самый продаваемый автопроизводитель в мире, Toyota считает, что сможет сократить разрыв с Tesla (TSLA.O) и другими компаниями, сочетая новые технологии с известными методами бережливого производства, которые она использовала в течение десятилетий для устранения неэффективности и избыточных затрат.
На недавней экскурсии по своему заводу в центральной Японии автопроизводитель продемонстрировал свои последние достижения, а также примеры экономной изобретательности, включая технологию изготовления глянцевых бамперов без использования краски.
Форма бампера вручную полируется до зеркального блеска, что придает ему блеск. В других частях завода оборудование, используемое для обработки деталей, теперь может работать ночью и в выходные дни благодаря автоматизации с помощью робототехники и 3D-моделирования, что, по словам представителей Toyota, привело к тройному увеличению производительности оборудования.
«Сила производства Toyota заключается в нашей способности реагировать на изменения времени», — сказал журналистам Казуаки Синго, директор по производству, во время экскурсии.
Он обратил внимание на инженерный и технологический опыт, основанный на «TPS» — сокращенном обозначении производственной системы Toyota.
Toyota революционизировала современное производство, создав систему бережливого производства, точной доставки продукции и организации рабочего процесса по принципу «канбан». Ее методы с тех пор начали использоваться повсеместно — от больниц до компаний, занимающихся программным обеспечением, и широко изучаются в бизнес-школах и на заседаниях советов директоров по всему миру.
Непрерывное стремление к совершенствованию и сокращению затрат способствовало восхождению Toyota от новичка послевоенного периода к мировому гиганту. Однако в производстве аккумуляторных электромобилей ее превзошла компания Tesla — другой неутомимый новатор — компания, которая благодаря своей эффективности достигла лидерства на рынке.
Под руководством нового генерального директора Кодзи Сато компания Toyota в июне объявила о амбициозном плане по расширению производства аккумуляторных электромобилей, что является значимым сдвигом после долгой критики в адрес производителя гибридного автомобиля Prius за его медленное освоение полностью электрических технологий.
По данным Goldman Sachs, в июне японский автопроизводитель займет лишь 0,3% мирового рынка электромобилей в 2022 году, назвав более мощное предложение «недостающим элементом» в своем модельном ряду.
Это не единственная автомобильная компания, сталкивающаяся с проблемами, связанными с переходом на электромобили. Детройтские автопроизводители «большой тройки» ссылаются на конкурентное давление со стороны Tesla и противодействуют требованиям профсоюза United Auto Workers по заработной плате, которые на прошлой неделе привели к беспрецедентной одновременной остановки.


СБОРОЧНЫЙ КОНВЕЙЕР, ГИГАКАСТИНГ
Одним из инновационных направлений, на которое особое внимание обращает компания Toyota, являются самоходные производственные линии, где электромобили перемещаются по конвейеру, управляемые датчиками. Эта технология позволяет устранить необходимость в использовании конвейерного оборудования, которое является одной из основных составляющих затрат в процессе сборки автомобилей, и обеспечивает большую гибкость производственных линий.
В ходе демонстрации электромобили передвигались без крыши, что облегчало установку компонентов. С помощью роботизированной системы Fanuc (6954.T) сиденья автомобилей устанавливались на шасси электромобилей. Рядом автономный погрузчик снимал сиденья с контейнера.
Toyota также представила прототип технологии литья под давлением, известной как «гигалитье». Эта технология была впервые использована компанией Tesla и позволяет изготавливать алюминиевые детали гораздо большего размера, чем те, которые ранее применялись в автомобильном производстве.
Подобно Tesla, Toyota заявляет о намерении производить электромобили модульными секциями, что позволит сократить количество деталей. Однако, Toyota также выделяет свои собственные инновации. Благодаря многолетнему опыту работы с литьем под давлением, компания разработала быстросменные формы, которые периодически требуются при гигалитейном производстве.
Toyota утверждает, что время замены формы сокращено до 20 минут по сравнению со стандартными 24 часами. По оценкам компании, это позволяет увеличить производительность на 20%.
На заводе Motomachi в городе Тойота автопроизводитель внедрил самоуправляемого транспортного робота, который перевозит новые автомобили по парковке площадью 40 тыс. кв. м (10 акров). Обычно эту работу выполняют водители перед погрузкой автомобилей на грузовики.
Водители грузовиков проходят за автомобилями в среднем 8 км (5 миль) в день, что сокращает время работы и увеличивает физическую нагрузку в условиях высокой текучести кадров.
Автопроизводитель заявил, что к следующему году на заводе Мотомачи будет работать 10 роботов, и затем рассмотрятся возможности внедрения на других заводах. Кроме того, роботы могут быть проданы другим компаниям.